On a day-to-day basis, slurry pump operators need to consider a range of critical factors, from particle size and flow rate to concentration and part wear. Among these is the phenomenon of pipe friction loss due to solids, which if not accounted for can affect the production bottom line. But what is friction loss? What causes it? And how can it be avoided?
Friction loss 101
Friction loss is the loss of head (or pressure) in a pipeline that occurs as a result of the resistance to flow which is present when the liquid or slurry moves through it. This loss can negatively impact the overall flow rate and reduce the system’s delivered tonnages. Over time, friction losses can have costly consequences and make an otherwise finely tuned slurry operation inefficient. By calculating friction losses properly, an operator can minimize them and ensure that their pump operates at the desired duty point.
What makes friction loss so critical — and sometimes difficult to predict — is the complex interaction between the solids and flow field. Additionally, there are a lot of variables which affect the friction losses; friction loss varies with pipe diameter, pipe length, pipe material, and slurry flow rate, as well as whether the flow is laminar or turbulent, among other factors. In straight pipes, friction losses are called major losses. In non-straight pipes or bends, losses are called minor losses. Typically, as the names imply, minor losses are small in relation to major losses.
Although operators can determine friction loss manually with the help of graphs, formulas, and tables, factors such as frequent changes in processes and operation can make calculation and predictions difficult to perform in a way that allows for effective operability of the pipeline. Fortunately, operators can better manage friction loss by answering a simple question: Is my slurry settling?
Settling slurries
Whether a slurry is settling or non-settling impacts how and to what degree friction losses occur. Settling slurries are low in viscosity and have relatively large particles that tend to accumulate at the bottom of the pipe when operating within the industrially relevant range of pipe velocities and turbulence levels. At low velocities, the solids can settle and block the pipe. At high velocities and at certain concentrations, in some cases, friction losses can be taken as equal to water losses, when expressed in height of slurry per unit length of pipe.
By comparison, non-settling slurries are typically relatively high in viscosity and contain small particles (under 50 microns in diameter) that don’t settle when operating within the industrially relevant range of pipe velocities and turbulence levels. Non-settling slurries come with even more variables than their settling counterparts, which makes manual assessment of friction losses without a-priori testing nearly impossible. Further complicating friction loss is the fact that non-settling slurries are usually non-Newtonian.
For Newtonian fluids, like water or gasoline, viscosity is constant at a given temperature. For non-Newtonians, like blood, paint, and many non-settling slurries, the viscosity varies with the strain (flow) rate at a given temperature. To establish friction losses for non-Newtonian slurries, pump operators must measure rheological parameters which describe the relationship between the shear stress and the strain rate for a given slurry — it’s impossible to calculate these parameters manually or without testing.
Mitigating friction loss
Friction loss can negatively affect a slurry transport system’s operability and result in lower delivered tonnages of solids than expected. In the long term, it can mean lost revenue. In the short term, however, system losses can be managed:
- Use proper fittings — In systems that use valves and fittings, operators must calculate and include a corresponding allowance for additional friction, because fittings can contribute to the pump’s total dynamic head. To account for and mitigate extra friction, calculate the minor losses with the use of loss coefficients (k values), and ensure the parts being used are the appropriate size.
- Track your variables — Although the many variables associated with slurries makes calculating friction losses difficult, you can most accurately predict the friction losses by determining and including in your calculations as many variables as you can, such as pipe diameter, particle size distribution, solids shape and density, and liquid viscosity and density, among others.
- Know your slurries — Different slurries have different characteristics that impact friction losses in different ways. Learn the difference between settling and non-settling slurries, as well as Newtonian and non-Newtonian fluids. Depending on what type of slurry you are pumping, different models must be used in order to accurately predict friction losses.
Friction loss doesn’t have to be the bane of every pump operator’s existence. With a little homework and attention, you can mitigate friction loss and ensure that your slurry pumps run smoothly!
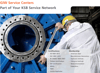