For nearly 130 years of operation, we’ve earned a reputation for reliability and trust — and our talented technical services team is a big part of that success. All customers receive the same level of dedication and comprehensive, round-the-clock service from pump selection and set-up through years of operation. What kind of technical services do we provide?
Installation and start-up
Before our customers can start their operation, they need to ensure that their final assembly is installed and aligned properly. These assessments may require more insight than the manual can provide on its own. That’s why our experts provide technical support for every aspect of pump assembly and alignment — so our customers can be certain that their pump system is set up exactly according to their needs.
Of course, a properly assembled pump is only effective if the customer knows how to use it. Without the right operator training, the pump is essentially useless. To address this need, we ensure our customers have a complete understanding of how their pump works, section by section, before starting operation. We also train customers on assessing and maintaining components, including the motor, couplings, and gearbox. Start-up services should be requested 30-60 days in advance.
Field issues and troubleshooting
No matter what issues our customers face in the field, we are there to help. Our Technical Services are available around the clock to support any and all of our products and customers. Technicians from KSB GIW, Inc. take the lead on any maintenance and equipment issues, leaving customers free to handle other business. We also fulfill warranty claims in a quick, hassle-free manner.

It’s this kind of reliability and commitment that our customers have come to expect and rely on. We are committed to providing our customers with consistent and reliable service when and where our customers need us, whether that’s in person or over the phone. This level of service allows us to remain a part of our customer’s business for the long term — and it shows with each interaction.
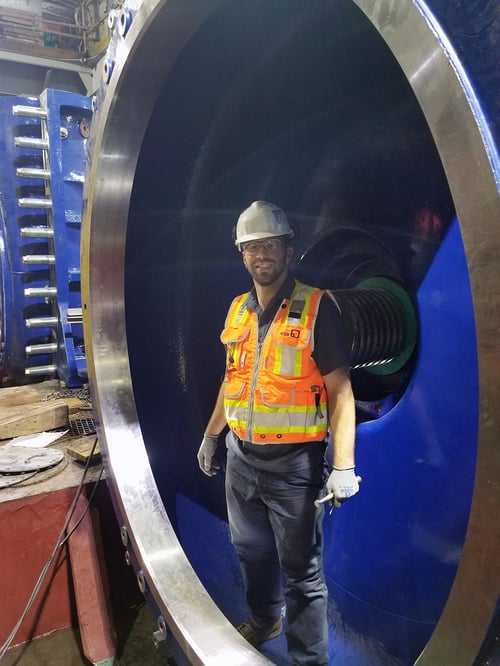
Training and other services
Beyond our Technical Services, KSB GIW, Inc. is committed to providing continuing education to our customers and their teams. This education comes in the form of classes for engineers at our headquarters in Grovetown, GA — including our Maintenance course and Slurry Transport course — which are held annually. We also offer regular site visits to address customers’ needs and keep their team members up to date on the best in pump technology. Our courses can be adapted to fit their class sizes as well! Our services include laser alignment, vibration analysis, installation guidelines to prevent soft foot, and more. No matter what our customers need, we are committed to serving them at every stage of their pump’s life. This includes installation, maintenance, and future upgrades.